Datanomix secures $12M in growth funding to expand its production intelligence platform for industrial manufacturers
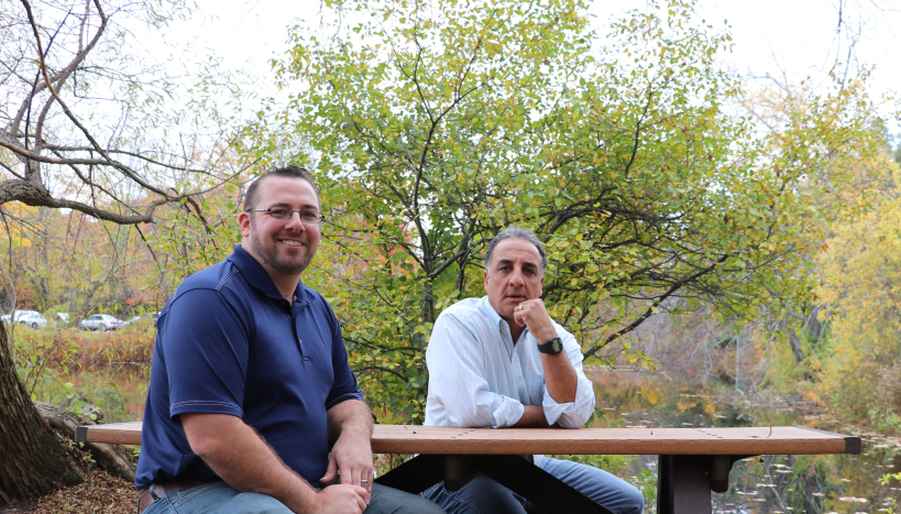
It feels like just yesterday, but it has been four years since our last coverage of Datanomix. Back then, the Nashua, New Hampshire-based startup, which provides operational insights to industrial manufacturers through its manufacturing analytics platform, raised $2 million in funding to drive the commercialization efforts and advance the development of its Fusion product. The company has since grown multiple folds.
Fast forward four years later. Datanomix announced today that it raised $12 million in new growth funding led by MK Capital and Joint Effects, with participation from multiple Datanomix customers, Hub Angels, and previous investors like PBJ Capital, Gutbrain Ventures, and CEAS Investments. In conjunction with the funding, Datanomix also announced that Mark Koulogeorge of MK Capital will join its Board of Directors.
Founded in 2017 by enterprise data veterans John Joseph (CEO) and Greg McHale (CTO), Datanomix offers a manufacturing Analytics platform that combines machine data streams from your shop floor into actionable insights for your top floor. Focused on the global Industry 4.0 and Industrial Internet of Things (IIoT) digital transformations.
Datanomix’s mission is to provide operational insights to industrial manufacturers and deliver Production Intelligence for the Next Generation by offering high-quality and high-impact solutions that are low-burden for users. Among its flagship offerings are the No Operator Input Production Monitoring platform and Digital GEMBA Boards.
In a statement, Joseph said, “Over the last two years, Datanomix has taken the market by storm with significant customer growth and product leadership. Our No Operator Input™ approach to production monitoring, which does not burden operators with any data entry, frankly awoke a sleeping market that has been waiting for innovation. We are proud that our brand has been recognized by leading customers, partners, and investors for the differentiation and impact we are providing to industrial manufacturers.”
Production monitoring as a category has been largely focused on asset utilization and downtime reason code collection. However, Datanomix has pioneered a new way to look at productivity in manufacturing environments called “No Operator Input” which eliminates the need for downtime reason codes, reduces the burden on operators, and simplifies data integration requirements.
The new approach also helps manufacturers manage their factory environments through a novel production scoring system, allowing a rapid response to the most pressing problems.
“When Datanomix arrived on the scene, production insight had stagnated,” said Kylan Hastreiter, Vice President at Hastreiter Industries. “ERP systems had not evolved, and still only gave high-level job stats after the fact, when it was too late to make improvements. Some monitoring systems had their user interfaces slightly updated, but the methodology was unchanged from the last decade where raw data is collected, operators are tasked with tedious data entry and tagging, and interpretation is left to manufacturing personnel who are already overloaded. Real-time, zero-burden insights were the gap that needed to be closed, and Datanomix has delivered that.”
Greg McHale, Co-Founder and CTO at Datanomix, added, “We spent hours with manufacturers who were using prior-generation monitoring systems, and saw exactly why operator input, complex integrations, and asset utilization alone were not transforming how they ran their businesses. While the category is called production monitoring, this is really about production management. Monitoring is a passive word, and people get into monitoring not to be passive, but to actively manage their operations better. What the market was missing was a vendor who believed it was their responsibility to provide context, insight, and impact that causes people to get out of their chair and respond because of what has been uncovered in their production data.”