Logmore Looks to Streamline Pharmaceutical Supply Chain Operations after Successful Series A
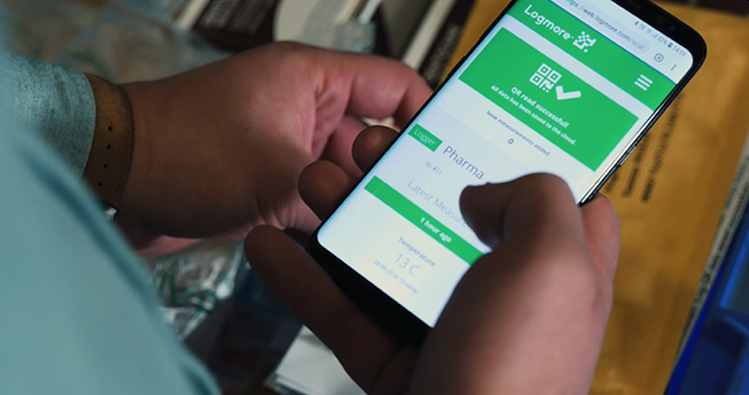
By 2024, the global pharmaceutical industry is expected to become a $1.18 trillion market fueled by innovation and increasing demand. However, this growth also comes with certain challenges. Its supply chains, in particular, must be able to cope.
Certain raw materials used in the manufacture of drugs and even end products must be kept and handled within certain conditions to ensure their safety and efficacy. Unfortunately, issues arising from temperature-controlled supply chains or “cold chains” lead to rejects and waste. The pharmaceutical industry loses at least $15 billion per year due to cold chain failures.
Condition-monitoring company Logmore looks to solve this by helping pharma cold chains improve their quality control through its data-logging service. The company provides QR tags that can monitor data such as temperature and humidity of shipments and packages. It recently raised €4.5 million in a Series A funding round led by NordicNinja VC to expand its market in North America, Asia, and Europe. Logmore is currently being used by more than 150 enterprises across various industries that require logistics quality controls including pharma, food, and electronics.
Cold Chain Challenges
Quality assurance in the pharmaceutical industry is a highly critical function as it ensures that the drugs that are used by patients are safe and effective. As such, the industry is heavily regulated. Governing bodies such as the United States’ Food and Drug Administration (FDA) have imposed regulations to ensure that companies follow temperature guidelines.
For pharmaceutical shipment of temperature-sensitive materials, distributors must typically maintain a 2°C to 8°C range all throughout the delivery process. However, some pharma products require cryogenic freezing (below 0°C temperature ranges) or controlled room temperature (15°C to 25°C). Falling outside of a specified range can render these products useless.
To comply, pharma companies typically use insulated containers and refrigerators to deliver their products. However, these are not foolproof. Other variables can affect the shipment. For example, temperature and humidity can sometimes quickly change because of extreme weather conditions. Pharma products can freeze in cold climates or spoil when exposed to high temperatures. The slightest gaps in damaged containers can cause temperature variations and expose drugs and medicine to unacceptable conditions that can lead to spoilage.
To avoid failures in temperature-controlled shipments, companies are investing in specialized packaging and storage units to ship their products. Pharma cold chain logistics spending is predicted to grow to over $16.6 billion by 2021.
How Condition Monitoring Can Help
Despite significant investments in the improvement of cold chains, issues can still arise. The biopharma segment alone still loses approximately $35 billion annually due to temperature failures in the supply chain. As such, pharmaceutical companies must find other ways to minimize waste.
Solutions such as Logmore are now available to help pharma companies improve quality control in their supply chain through its data logger. Its QR tags are equipped with built-in sensors that can log various condition data such as temperature, humidity, tilt, shocks, and ambient light, and allow pharma companies to monitor the status of their shipment and packages.
Logmore’s data logger can be scanned using a standard mobile device camera or a QR scanner. The information can then be uploaded to the cloud without need for USB port connections. Companies can readily access condition data so that they can ensure that their shipments are compliant with regulations. Accurate documentation ensured by the information can also help companies pinpoint areas for improvement of their cold chains.
Having access to timely information also enables companies to timely act on issues. They can readily track down shipments and verify when conditions change in real time. They can notify their logistics teams regarding any concerns. They can also immediately change routes and schedules, and even replace storage units if needed. Minimizing cold chain issues can ultimately mitigate rejects and waste.
Helping Pharma Companies Minimize Waste
Improving condition monitoring in the supply chain brings benefits to pharmaceutical companies and their consumers. Using condition-monitoring solutions, pharma companies can minimize waste, which translates to bigger profit margins. Consumers are also guaranteed a reliable service that ensures they receive safe and effective drugs to treat their conditions. The reduced costs should allow pharma companies to offer their products at more affordable prices, making them more accessible to those in need.
Want Your Story Featured?
Get in front of thousands of founders, investors, PE firms, tech executives, decision makers, and tech readers by submitting your story to TechStartups.com.
Get Featured